Manual labeling can be tedious, slow, and prone to errors, making it a challenge for businesses aiming for efficiency. As production increases, maintaining accuracy and speed becomes harder. The solution to these issues is an automatic label applicator, which enhances efficiency, reduces mistakes, and lowers long-term operational costs.
Automatic label applicators for round containers are a wise choice as they offer faster production, improved accuracy, and lower labor costs compared to manual methods. They streamline the labeling process, increase throughput, and minimize human error, resulting in cost savings and a higher quality of output.
Now let’s explore why an automatic labeling system can be a game-changer for your business.
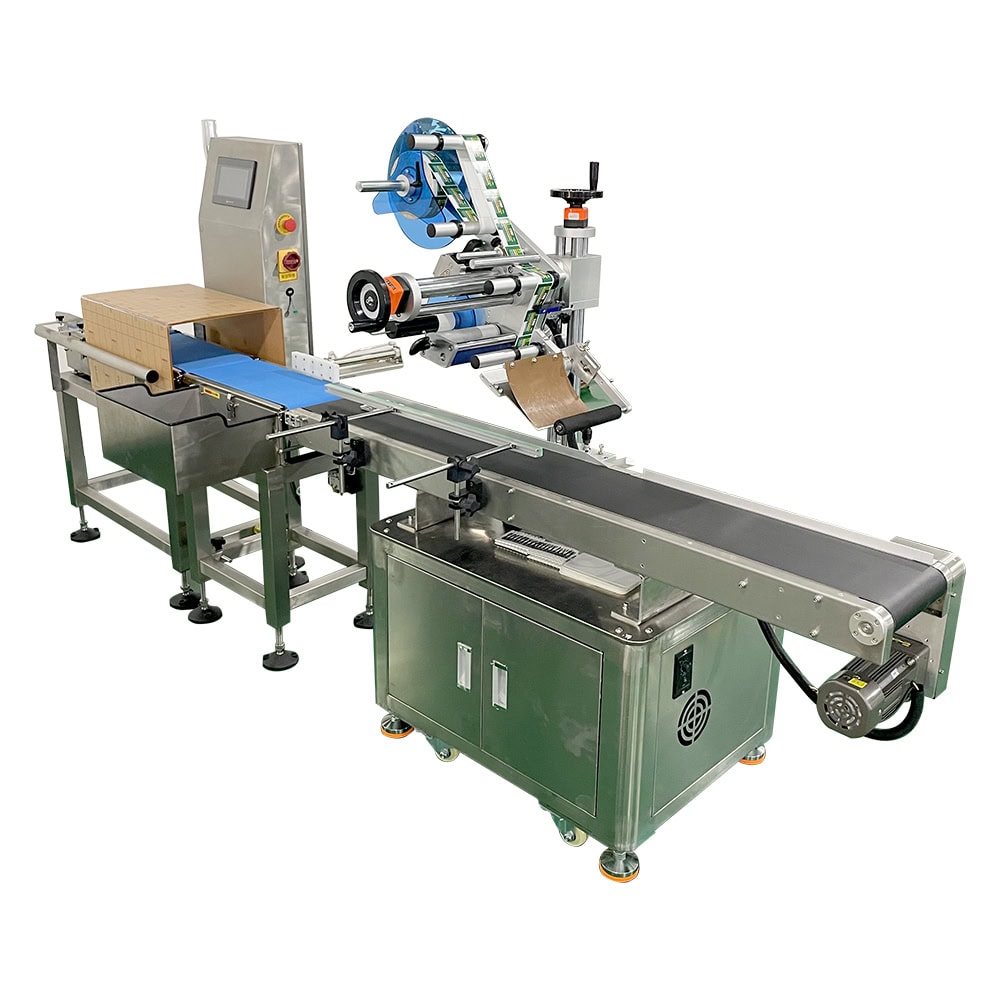
Why Is Speed Critical in Labeling Round Containers?
Speed is a critical factor in the manufacturing process, especially when labeling round containers. High-speed production lines require an efficient system to avoid bottlenecks and ensure a smooth workflow.
Automatic labeling machines significantly outperform manual systems in terms of speed. They can label thousands of containers per hour, which is essential for businesses that need to meet high production demands.
Automatic systems are designed to handle large volumes efficiently. For instance, an industrial automatic labeling machine can label up to 6,000 containers per hour, while manual systems can handle far fewer, leading to delays. This speed advantage is crucial in industries such as food packaging, pharmaceuticals, and beverages, where high throughput is required.
Additionally, automatic systems reduce downtime between product changes. Many machines feature quick-changeover capabilities, allowing for fast adjustments between different container sizes or types without slowing down production.
Speed Factors:
- Volume Handling: Automatic systems can manage varying production volumes, from small batches to large-scale operations.
- Labeling Time: Machines can apply labels in seconds, increasing overall production speed​.
- Reduced Downtime: Quick changeovers ensure that production is never delayed when switching between product types.
How Does Automation Improve Labeling Accuracy?
Inaccurate labeling can result in wasted products, customer dissatisfaction, and brand damage. Automatic labeling systems excel at ensuring high precision, which is essential for maintaining product quality.
Automatic label applicators provide precise label placement every time, reducing the chances of misalignment and costly labeling errors.
Automatic labeling systems are equipped with advanced sensors and calibration tools that detect and correct label misplacement before it becomes an issue. Unlike manual labeling, which depends on human skill and consistency, automatic machines can deliver perfect label placement regardless of the size or shape of the container.
For example, a round bottle labeling machine can detect the exact spot for the label and apply it perfectly aligned every time. This level of accuracy is critical in industries like pharmaceuticals or cosmetics, where even a small mistake can lead to product recalls or customer complaints.
Error Prevention:
- Misalignment: Automatic systems ensure that labels are applied straight and correctly aligned​.
- Consistency: These machines maintain high-quality output over long production runs without the variation that can occur in manual processes​.
What Are the Cost Benefits of Switching to Automatic Labeling?
Switching from manual to automatic labeling requires an upfront investment, but the long-term savings are significant, making it a cost-effective solution.
While automatic systems may have a higher initial cost, they save money in the long run through reduced labor costs, fewer errors, and improved efficiency.
Manual labeling requires ongoing labor costs, while automatic labeling reduces the need for human operators. This can lower staffing requirements and allow workers to focus on more important tasks, such as quality control or machine maintenance. Over time, the savings on wages and reduced labeling errors can offset the higher initial purchase price of the labeling machine.
For example, a fully automated bottle labeling machine can apply labels without human intervention, saving on labor costs and minimizing the chances of human error, which can lead to wasted labels and product defects.
Cost Considerations:
- Initial Investment: Automatic machines may cost more upfront, but they offer better long-term value.
- Operational Savings: Fewer errors and less labor required reduce ongoing operational costs​.
Why Is Automation More Flexible than Manual Labeling?
Flexibility is a major advantage of automatic labeling systems. With the capability to handle various types of containers and labels, they adapt to changing production needs without sacrificing speed or quality.
Automatic labelers can quickly adjust to different container sizes and shapes, allowing businesses to remain agile in a dynamic market.
An automatic labeling system can handle a variety of products, whether it’s a bottle, a jar, or a uniquely shaped container. Many modern machines feature electronically controlled adjustments that can be saved for future use. This means that once the settings are configured for a specific product type, they can be recalled instantly for future runs, reducing downtime during transitions.
This flexibility is especially beneficial in industries where product lines are frequently updated, and the ability to handle multiple container types without requiring major retooling is a major time-saver.
Flexibility in Design:
- Container Variety: Automatic systems are adaptable to a range of containers, from standard bottles to unique shapes​.
- Quick Recalibration: Recalibration for different labels or containers can be done quickly, ensuring smooth transitions between product batches​.
Conclusion
Investing in an automatic label applicator for round containers is a smart decision that offers faster production, greater accuracy, and long-term cost savings. The flexibility, reduced labor costs, and improved efficiency make it a valuable addition to any production line.