Inconsistent bottle labeling can cause production delays and compromise product quality, making it vital to optimize every aspect of the labeling process.
Stable bottle feeding, precise positioning, and responsive sensors are essential for efficient and accurate labeling.
By addressing these factors, businesses can enhance productivity, ensure consistent quality, and streamline operations. Here are the key considerations.
Stable and Even Bottle Feeding
Smooth bottle feeding is crucial for maintaining a consistent production flow.
- Why It’s Important: Uneven feeding can disrupt the labeling process and lead to misalignment or missed bottles.
- Tips for Optimization: Use a well-calibrated bottle unscrambler to ensure consistent bottle spacing and alignment on the conveyor.
Precise Label Placement with Positioning Features
To achieve perfect alignment, labeling machines must be configured for precise label placement.
- Positioning Adjustments: Use sensors or mechanical guides to align bottles accurately. For bottles requiring labels at a specific angle, employ a positioning bottle labeling machine for optimal results.
- Advanced Techniques: Consider machines with automated positioning features to save time and improve accuracy.
Sensitive Label Sensors for Accurate Application
The responsiveness of label sensors determines how accurately labels are applied.
- Calibration Needs: Regularly calibrate the sensors to ensure they detect bottles and trigger label dispensing accurately.
- Preventative Measures: Clean the sensor area frequently to avoid errors caused by dust or residue.
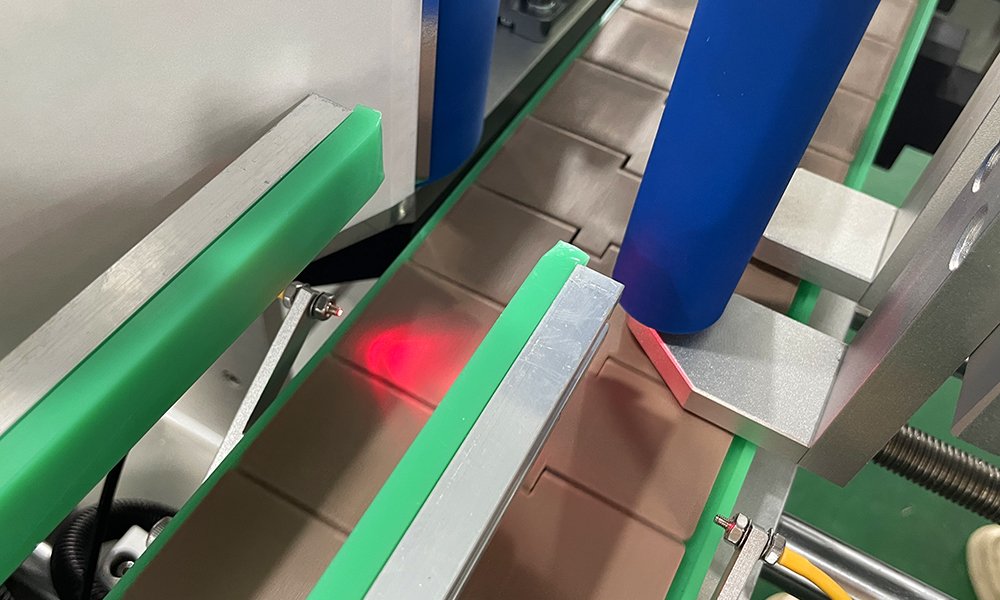
Regular Maintenance of Rollers and Belts
Keeping rollers and belts in excellent condition ensures smooth label application.
- Maintenance Tips: Inspect rollers for wear and clean them regularly to remove adhesive buildup. Replace worn belts to avoid slippage or misalignment.
- Proactive Checks: Schedule routine maintenance to prevent unexpected downtime.
Avoiding Label Wrinkles or Bubbles
A seamless finish is vital for maintaining a professional appearance.
- Tension Adjustments: Ensure the label roll is properly tensioned to prevent wrinkles. Adjust the peeling plate for a smooth label release.
- Surface Preparation: Clean the bottle surfaces to promote strong adhesive bonding.
Managing Bottles of Different Shapes and Sizes
Labeling bottles of varying dimensions can be challenging without proper adjustments.
- Custom Settings: Configure the machine to handle specific bottle shapes and sizes. For irregular containers, consider using a customized labeling machine to meet unique requirements.
- Operator Guidance: Train operators to make quick adjustments for different bottle profiles.
Optimizing Label Adhesion for Material Types
The label’s adhesive must match the material of the bottle to ensure durability.
- Material Considerations: Select adhesives compatible with glass, plastic, or metal bottles. Test adhesion under various storage conditions.
- Pro Tip: For certain materials, pairing the labeling process with a shrink wrap machine can enhance durability and presentation.
Control of Environmental Factors
External conditions can affect the labeling process and adhesive performance.
- Environmental Control: Keep the workspace temperature and humidity within recommended levels. Dust covers and air filters can minimize contamination.
- Long-Term Benefits: Controlled conditions extend the lifespan of equipment and improve label quality.
Operator Training and Safety Protocols
Skilled operators are essential for maintaining high efficiency and safety.
- Training Requirements: Provide in-depth training on machine operation, troubleshooting, and maintenance.
- Safety Measures: Ensure operators follow all safety protocols, especially when handling high-speed machinery.
Enhancing Efficiency with Auxiliary Equipment
Pairing a labeling machine with complementary systems can improve overall efficiency.
- Suggested Pairings: Combine with a bottle filling machine or a capping machine for a fully integrated production line.
- Streamlined Workflow: Auxiliary equipment reduces manual intervention and enhances throughput.
Conclusion
By focusing on these considerations, you can achieve consistent, high-quality labeling while maximizing the efficiency of your bottle labeling machine.