Inconsistent labeling can cause product recalls, compliance failures, and damage to brand reputation. This results in costly delays and fines. Labeling machines provide high precision and consistency, ensuring smooth operations and regulatory compliance.
Labeling machines maintain accuracy and consistency by using advanced sensors, precision motors, and automated control systems, which minimize errors, optimize speed, and ensure consistent results across various product types and surfaces.
With the right technology, labeling machines deliver accuracy and consistency, helping businesses maintain product quality and efficiency.
Advanced Sensor Technology
Labeling machines are equipped with advanced sensors, such as electric eyes, that detect product presence and ensure accurate label placement. These sensors play a crucial role in minimizing misalignment and ensuring the labels are applied in the correct position every time. For instance, flag labeling machines use sensors to detect label gaps, ensuring each label is placed precisely, even in high-speed operations. This level of precision is essential for industries where regulatory standards must be met.
Additionally, these sensors can handle a wide range of label types, including self-adhesive labels and barcodes, making them highly adaptable for different industries. They also help reduce downtime by detecting potential issues like missing labels before they cause a production halt.
High-Precision Motors
Stepper motors and servo motors in labeling machines provide the precise control necessary for accurate label application. These motors control the movement of the labels with minimal variation, ensuring that every label is applied with the same level of accuracy. The precision offered by these motors is vital for businesses looking to scale up their operations while maintaining quality.
For example, in the case of a bottle labeling machine, high-precision motors help maintain consistent label placement across different bottle sizes and shapes. This level of control is essential for high-speed production lines, where even small errors can lead to significant wastage.
Automated Control Systems (PLC Integration)
Most modern labeling machines are integrated with Programmable Logic Controllers (PLCs) that oversee the entire labeling process. PLCs control the timing and sequence of the labeling operation, ensuring each step happens at precisely the right moment. This level of automation allows for real-time adjustments, ensuring consistency across production runs.
In industries using packaging machines, the integration of PLC systems ensures that the entire packaging process, from labeling to sealing, operates smoothly and consistently. Automated systems reduce the likelihood of human error and make it easier to achieve a high degree of accuracy, even in complex operations.
Adjustable Settings for Customization
Labeling machines offer flexible settings to accommodate different product sizes and label types. This adaptability allows businesses to use the same machine for multiple products without compromising on accuracy. Operators can adjust label size, application speed, and position based on the specific requirements of each product.
For instance, a customized labeling machine can be tailored to fit the unique requirements of specific industries, such as pharmaceuticals or electronics. This flexibility ensures that the machine can handle a variety of products while maintaining the same level of precision.
Consistency in Data Labeling
In industries such as machine learning, consistency in data labeling is critical. Labeling machines used in these environments must follow strict guidelines to ensure data accuracy. Consistent labeling helps reduce bias and errors, improving the overall quality of data, which is essential for training machine learning models.
In these scenarios, accurate label application is critical not only for physical products but also for data-driven processes. The precision and consistency offered by these machines allow for large-scale operations without the risk of inconsistent results.
Real-Time Feedback Systems
Many labeling machines are equipped with real-time monitoring and feedback systems that detect issues like misalignment, missing labels, or jams. These systems provide immediate alerts, allowing operators to correct the problem quickly and prevent downtime. This capability ensures that the labeling process continues smoothly and without interruptions.
For example, a barcode printer integrated with real-time feedback systems can immediately identify and rectify any issues with label printing or placement, ensuring that each barcode is applied accurately and can be scanned without errors.
Durability and Maintenance
Durability plays a crucial role in ensuring that labeling machines maintain their accuracy over time. High-quality components, such as stainless steel rollers and durable tension mechanisms, reduce the risk of wear and tear, which can lead to inconsistencies in label application. Regular maintenance is also essential to keep the machine operating at peak efficiency.
Businesses that invest in durable machines, such as a vacuum packaging machine, benefit from longer-lasting equipment that requires less frequent repairs. Regular maintenance schedules ensure that the machine remains calibrated and accurate, preventing potential issues before they affect production.
Compliance with Industry Standards
In industries such as pharmaceuticals and food production, regulatory compliance is essential. Labeling machines ensure that all required information—such as expiration dates, barcodes, and batch numbers—is printed accurately on each product. This reduces the risk of recalls and legal penalties.
For example, filling machines used in food production must adhere to strict labeling standards to ensure that nutritional information and expiration dates are accurately displayed. Labeling machines in this context help maintain compliance with industry regulations, ensuring product safety and consumer trust.
Scalability and Speed
As businesses grow, their production needs increase, and maintaining accuracy across larger production volumes becomes challenging. Labeling machines designed for high-speed operations can maintain precision even when handling thousands of labels per hour. This scalability is essential for companies looking to expand without compromising on quality.
Machines like the corner wrap labeling machine can apply labels to products at high speeds, ensuring that the accuracy and consistency of labeling are maintained even as production scales.
Adaptability for Different Product Types
Labeling machines are designed to handle a wide variety of products, from bottles and boxes to wires and cables. This adaptability ensures that the same machine can be used across multiple product lines without losing accuracy. For instance, wire labeling machines apply labels to small-diameter wires with the same precision as they do for larger cables.
The ability to handle different product types, such as with a flat labeling machine, ensures that businesses can maintain consistent labeling across their entire range of products.
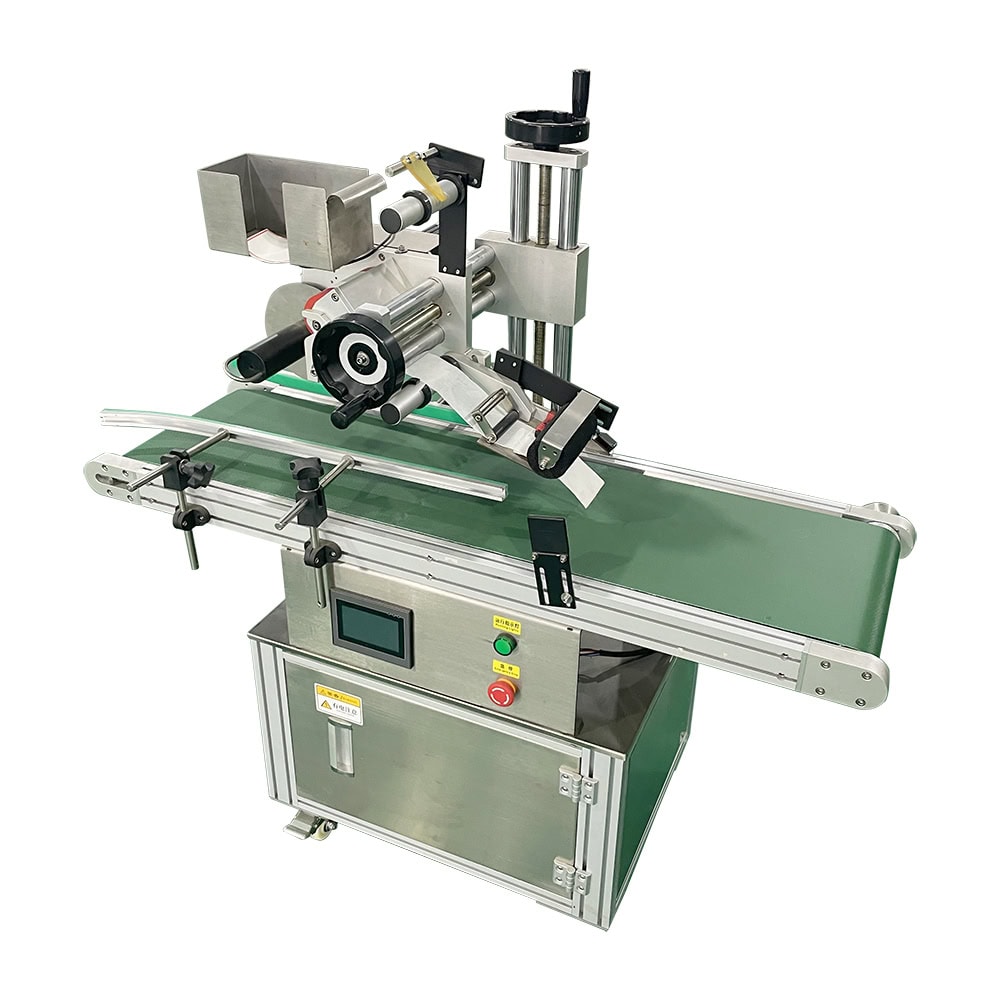
Traceability and Accountability
Labeling machines play a key role in ensuring that products can be traced throughout the supply chain. By accurately applying barcodes and other identifying information, these machines make it easy to track products from production to distribution. This traceability is essential for quality control and regulatory compliance.
For example, integrating a barcode printer into a labeling system allows companies to track their products at every stage, ensuring that any issues can be identified and resolved quickly.
User-Friendly Interfaces and Training
Modern labeling machines are equipped with user-friendly human-machine interfaces (HMIs) that allow operators to easily input parameters and monitor the labeling process. Proper training ensures that operators can effectively use the machine, reducing the likelihood of human error and improving overall consistency.
Machines like the taping machine come with simple, intuitive controls that make it easier for operators to adjust settings and troubleshoot issues, ensuring smooth and accurate labeling operations.
Conclusion
Labeling machines guarantee accuracy and consistency through the use of advanced sensors, precision motors, and customizable automated controls. These features provide a seamless labeling process across various industries, ensuring quality and compliance at every stage of production.