Packaging boxes efficiently is a critical step in many industries, yet manual sealing methods often lead to inconsistent results and inefficiencies. Automating this process with a case taping machine can solve these challenges by ensuring speed, precision, and uniformity in sealing.
Case taping machines automate the process of sealing boxes using adhesive tape, offering consistent and efficient solutions for industrial packaging.
Understanding their components and workflow helps businesses optimize their packaging processes, enhancing productivity and reducing costs.
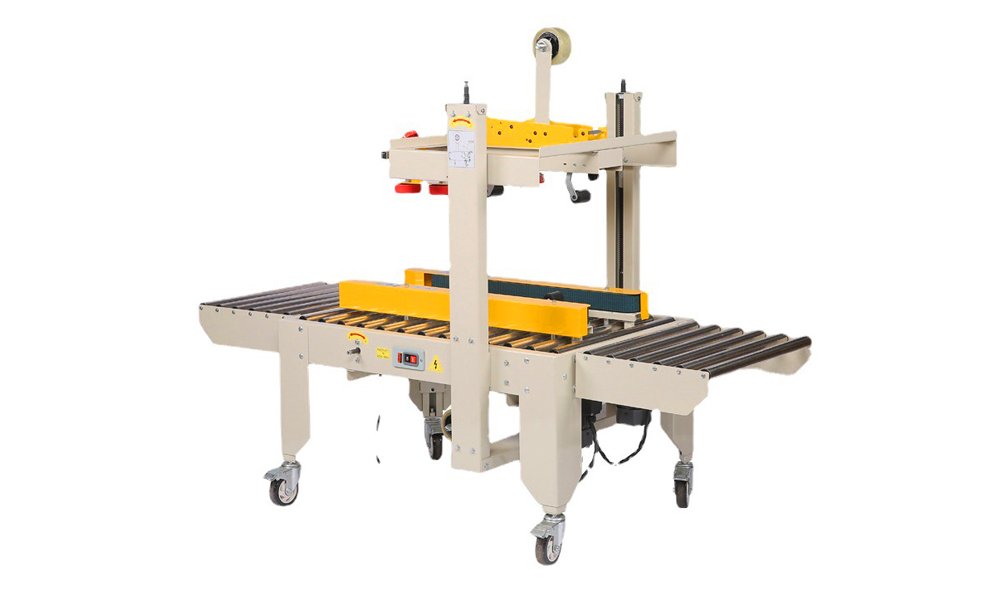
Components of a Case Taping Machine
1. Frame and Conveyor System
The sturdy frame supports the machine while the conveyor system transports boxes through the sealing process. Adjustable conveyor belts ensure smooth and reliable box movement.
2. Tape Dispenser
The tape dispenser holds rolls of adhesive tape and applies them to the boxes. It is designed to maintain consistent tension for an even application.
3. Adjustable Guides
Guides align boxes as they move through the machine, ensuring the tape is applied to the correct areas, regardless of box size.
4. Drive Belts or Rollers
These components maintain box stability and propel them through the sealing station at a controlled speed.
5. Cutting Mechanism
After the tape is applied, a sharp blade cuts the tape to the correct length, leaving a clean and professional finish.
How Case Taping Machines Operate
1. Box Placement
Operators place filled boxes on the machine’s conveyor system. Some machines, like the taping machines, work seamlessly with automated feeding systems for higher throughput.
2. Alignment and Adjustment
Adjustable guides position the box securely, ensuring tape application aligns perfectly with the box seams.
3. Tape Application
The tape dispenser applies tape to seal the box’s top and/or bottom as it passes through the machine.
4. Tape Cutting
A blade cuts the tape at the end of the sealing process, creating a neat and secure seal.
5. Sealed Box Exit
The sealed box exits the machine and is ready for labeling, shrink wrapping, or distribution.
Types of Case Taping Machines
Uniform Case Sealers
These machines are ideal for operations with boxes of the same size. Manual adjustment is required when switching box dimensions.
Random Case Sealers
Designed to accommodate varying box sizes without manual intervention, these machines are excellent for production lines with mixed packaging.
Benefits of Case Taping Machines
1. Improved Efficiency
Automating box sealing with a case taping machine significantly reduces manual labor, streamlining the packaging process.
2. Consistent Quality
Tape is applied evenly, ensuring secure seals that enhance product integrity during transit.
3. Cost-Effectiveness
Efficient tape usage and reduced labor costs contribute to long-term savings.
4. Versatility
Machines like industrial shrink wrap systems can complement taping machines, creating an integrated packaging solution.
Selecting the Right Case Taping Machine
1. Box Size and Variability
For uniform box sizes, choose a standard case sealer. Random case sealers are better suited for variable dimensions.
2. Production Volume
High-production lines benefit from fully automated systems, while smaller operations may opt for semi-automatic machines.
3. Integration Needs
Ensure compatibility with existing equipment such as vacuum packaging machines or conveyor systems for seamless operations.
Conclusion
Case taping machines simplify and standardize the box sealing process, making them indispensable for efficient packaging operations. By understanding their components, operation, and benefits, businesses can select the right equipment to enhance their workflow, improve product protection, and reduce costs.