In the fast-paced world of manufacturing and logistics, ensuring that wires are correctly labeled is crucial for both safety and efficiency. However, choosing the right electrical wire labeling machines can be challenging due to the various questions and concerns potential buyers have.
To help you make an informed decision, we have compiled and answered twelve of the most common questions customers ask about electrical wire labeling machines. This guide aims to provide clarity and assist you in selecting the best equipment for your needs.
Understanding these key aspects will not only help you choose the right machine but also optimize your labeling process, ensuring smooth operations and compliance with industry standards.
Electrical Wire Labeling Machines
What Types of Wires Are Suitable for Electrical Wire Labeling Machines?
These machines are designed to handle a variety of wire types, including electrical wires, cables, and fiber optics. These machines are versatile and can label wires of different diameters and materials. This flexibility is crucial for industries such as automotive, telecommunications, and electrical installations, where precise and durable labeling is essential.
What Is the Range of Label Sizes That the Machine Can Handle?
These machines offer a wide range of label sizes to accommodate different wire diameters and labeling requirements. Typically, these machines can handle labels as small as a few millimeters to several centimeters in length. The ability to adjust label sizes ensures that each wire is properly identified without wasting label material or space.

Is the Operation of the Electrical Wire Labeling Machine User-Friendly?
Modern electrical wire labeler are designed with user-friendliness in mind. They feature intuitive interfaces, easy-to-follow instructions, and quick setup processes. Many machines come with touch-screen controls and pre-programmed settings that make the operation straightforward, even for users with minimal technical experience. This ease of use reduces the learning curve and increases productivity.
What Label Materials Are Available for Electrical Wire Labeling Machines?
The choice of label material is important for durability and readability. Electrical wire labeling machines typically support a variety of materials, including polyester, vinyl, and heat-shrinkable labels. Each material has its own advantages, such as resistance to chemicals, abrasion, and extreme temperatures. Selecting the right material ensures that labels remain legible and intact under different environmental conditions.
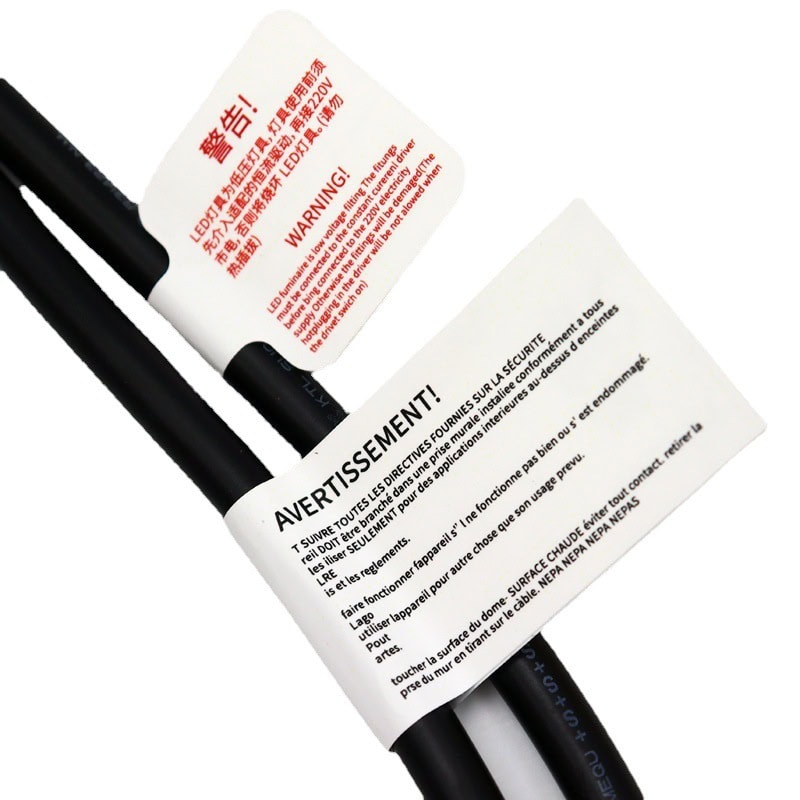
What Are the Maintenance Requirements for the machine?
Regular maintenance is key to the longevity and performance of electrical cable labeling machines. Basic maintenance tasks include cleaning the machine, inspecting and replacing worn parts, and ensuring that the software is up-to-date. Many manufacturers provide detailed maintenance guides and support services to help users keep their machines in optimal condition, reducing downtime and repair costs.
What Voltage Is Required for the Equipment?
These equipments are designed to accommodate different voltage requirements, depending on the country of operation. It is crucial to specify the voltage standards of your location when ordering a machine. Most manufacturers offer models that can operate on both 110V and 220V systems. Ensuring compatibility with various electrical infrastructures worldwide.

How Is the Equipment Transported?
Transporting the machines requires careful planning to ensure they arrive safely and in good condition. Manufacturers typically provide robust packaging solutions that protect the machine during transit. Additionally, they may offer shipping options that include insurance and tracking. Giving customers peace of mind that their investment is secure.
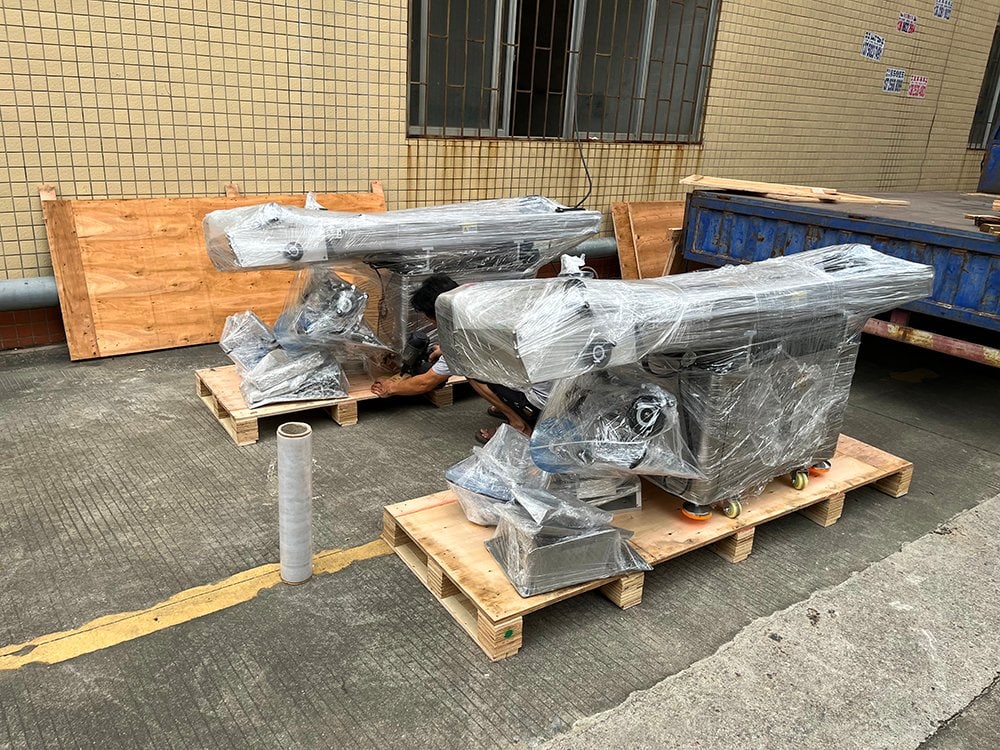
How Is the Equipment Packaged to Prevent Damage During Shipping?
Proper packaging is essential to prevent damage during shipping. They are usually packed in sturdy, shock-resistant containers with foam or padding to cushion any impacts. These measures help protect sensitive components and ensure that the machine arrives ready for immediate use. Manufacturers often have stringent quality control processes to verify that packaging meets high standards.
Do I Need to Calibrate the Equipment Upon Arrival?
One common concern is whether the equipment needs calibration upon arrival. Electrical wire labeling machines are generally pre-calibrated and tested before shipping. This means that once the machine is unpacked and set up. It should be ready for immediate use with minimal adjustments. This convenience saves time and ensures that you can start labeling wires right away.
Can You Provide Custom Label Solutions?
Many manufacturers offer custom label solutions to meet specific customer needs. This includes designing and producing labels with particular sizes, colors, and materials. Custom labels can enhance the efficiency and organization of your labeling process, ensuring that all wires are clearly and consistently marked according to your specifications.
What Should I Do if the Machine Breaks Down?
If an electrical wire labeling machine breaks down, the first step is to consult the troubleshooting guide provided by the manufacturer. Many issues can be resolved through simple fixes or adjustments. If the problem persists, manufacturers often offer remote support services to help diagnose and fix the issue. In cases where remote support is insufficient, on-site service may be required, which could involve additional costs.
Can the Machine Label Wires of Different Diameters Simultaneously?
These machines are capable of handling wires of different diameters. Especially if the diameter differences are not too significant. For wires with substantial diameter variations, adjustments may be needed to ensure optimal labeling. In some cases, custom labeling heads or settings may be required to accommodate a wide range of wire sizes effectively.
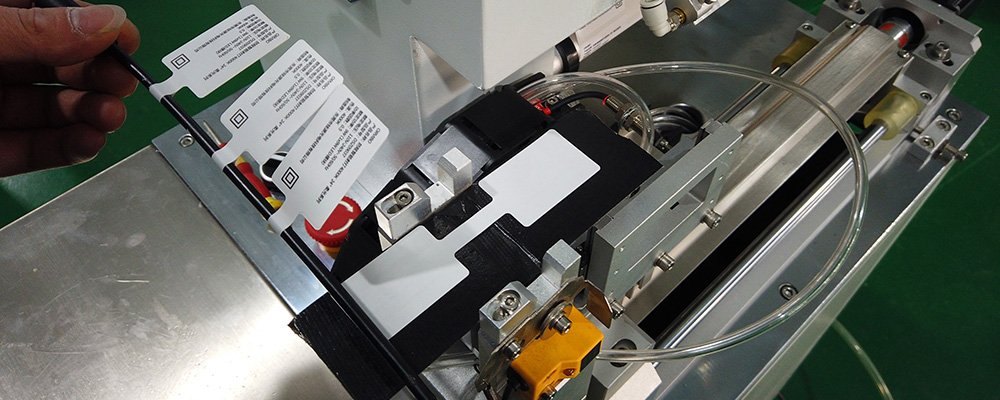
Conclusion
Choosing the right electrical wire labeling machine involves understanding the various features and capabilities that can address your specific needs. By considering these common questions and their answers, you can make a more informed decision and ensure that your wire labeling process is efficient, accurate, and reliable.