Manual liquid packaging can be time-consuming, inconsistent, and costly. A liquid packaging machine automates this process, boosting efficiency and ensuring consistent product quality.
A liquid packaging machine is an automated device designed to fill, seal, and package liquid products into containers of various shapes and sizes, offering precision, speed, and hygiene. These machines have transformed production lines in industries ranging from food and beverage to pharmaceuticals by streamlining the filling and sealing processes.
Let’s dive into how liquid packaging machines operate, their benefits, and how they support multiple industries in achieving higher productivity.
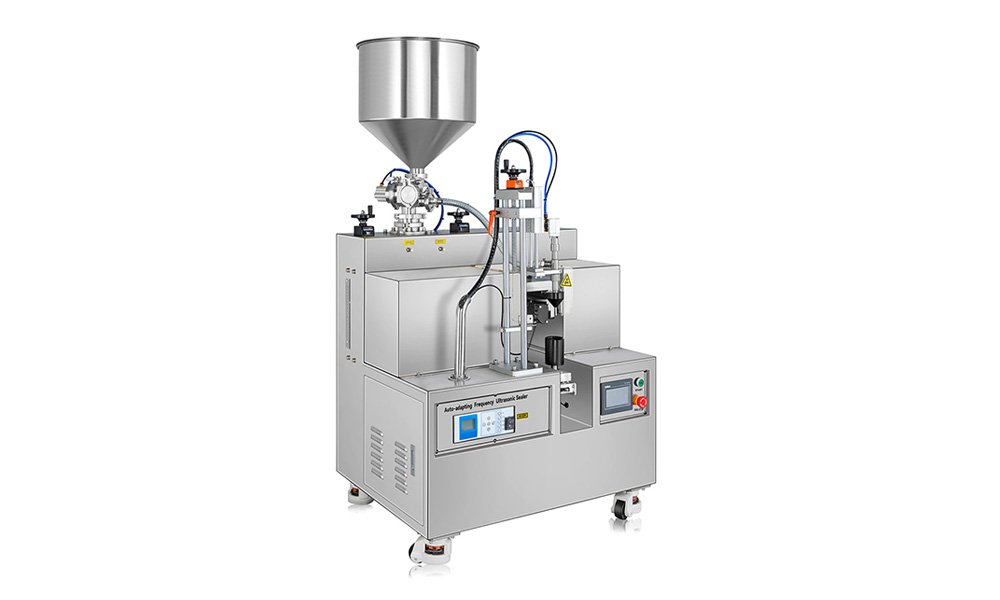
Benefits of Liquid Packaging Machines
Consistency and Precision
Liquid packaging machines ensure each container is filled to an exact level, critical in industries where accuracy is a necessity. For example, in the pharmaceutical and food sectors, maintaining precise quantities ensures product quality and regulatory compliance.
Increased Efficiency
By automating the packaging process, liquid packaging machines significantly reduce the time and labor costs associated with manual filling. This improvement enables businesses to produce higher quantities of finished products in shorter periods.
Versatility Across Liquids
These machines can handle a wide range of liquid viscosities, from water and thin juices to more viscous products like creams and syrups. With models that can be customized, such as a Liquid Filling Machine, companies can choose machines tailored to their product types, ensuring reliable performance across various liquid consistencies.
Reduced Waste and Cost Savings
By minimizing human error, liquid packaging machines help reduce product waste, resulting in considerable cost savings. Businesses benefit from a streamlined process that lowers operational costs while maximizing output.
Types of Liquid Packaging Machines
Gravity Fillers
Gravity fillers use gravity to control the filling process and are ideal for thin, low-viscosity liquids like water or clear juices. These machines operate efficiently and are often used in high-output production lines.
Pump Fillers
Pump fillers use pumps to control the liquid flow, making them suitable for thicker, more viscous liquids. The machine’s pump type can vary based on the liquid’s density, ensuring precise fills for items such as creams and sauces.
Piston Fillers
Designed for dense and thick products, piston fillers measure each fill using a piston mechanism. This type is ideal for products like gels, honey, and lotions, where consistency and accurate measurement are crucial.
Overflow Fillers
Commonly used for transparent containers, overflow fillers ensure uniform fill levels. They are ideal for products where aesthetic presentation, such as label alignment, is important.
Common Applications Across Industries
Food and Beverage
Liquid packaging machines are essential for bottling water, juices, sauces, oils, and dressings. Their accuracy is particularly valuable in the food industry, where consistent volumes are critical.
Pharmaceuticals
In the pharmaceutical sector, packaging machines handle liquid medicines like syrups, ensuring accurate dosages and hygienic packaging. Consistent fills prevent dosage discrepancies, vital for patient safety and compliance.
Cosmetics
Cosmetic manufacturers rely on liquid packaging machines to fill perfumes, lotions, gels, and creams. Consistency in fill levels is essential in cosmetics to maintain brand reputation and customer satisfaction.
Chemical Industry
In the chemical industry, packaging machines handle liquids like cleaning solutions and industrial chemicals. Machines are built with materials resistant to corrosion, ensuring durability when working with potentially hazardous substances.
Key Features and Technology in Liquid Packaging Machines
Programmable Logic Controllers (PLC)
Many liquid packaging machines use PLCs to automate and program various settings, enhancing the accuracy and speed of the packaging process. This system is particularly useful in high-volume production, where consistency is paramount.
Human-Machine Interface (HMI) Touchscreen
The HMI touchscreen provides a user-friendly interface for machine operators, allowing them to set parameters, monitor performance, and troubleshoot issues in real-time. This interface simplifies training and enhances operational efficiency.
Advanced Sensors
Modern liquid packaging machines come equipped with advanced sensors to ensure accurate fill levels and prevent jams or misfills. For instance, sensors in a Bottle Filling Machine detect when bottles are incorrectly positioned, halting the machine to avoid spillage or damage.
Material Compatibility
Liquid packaging machines are often made with corrosion-resistant materials, which is crucial when handling liquids like cleaning chemicals or acidic solutions. This compatibility enhances machine lifespan and operational reliability.
Automatic vs. Semi-Automatic Liquid Packaging Machines
Automatic Machines
Fully automatic liquid packaging machines complete the entire process from filling to capping and sealing without manual intervention. These machines are ideal for high-volume operations, ensuring maximum productivity with minimal labor requirements.
Semi-Automatic Machines
Semi-automatic machines require some manual input, often making them suitable for smaller or mid-scale production operations. They are versatile options for businesses seeking efficient production without fully automating their line.
Maintenance and Calibration of Liquid Packaging Machines
Routine Maintenance
Regular maintenance is essential to keep liquid packaging machines operating smoothly. Tasks such as cleaning nozzles, checking sensors, and lubricating moving parts help prevent breakdowns and ensure consistent performance.
Calibration for Precision
Calibrating the machine is crucial, especially for products with strict volume requirements. Periodic calibration ensures the accuracy of each fill, which is particularly important in the pharmaceutical and food industries, where precise measurements are critical.
Industries Benefiting from Liquid Packaging Machines
Industries such as food, cosmetics, chemicals, and pharmaceuticals experience significant productivity gains from liquid packaging machines. These machines ensure that products are packaged efficiently, maintain quality, and meet consumer demands. From the speed of a packaging machine in food and beverage settings to the accuracy of a filling machine in pharmaceuticals, the versatility of these machines serves countless applications.
Innovations and Trends in Liquid Packaging Machines
Eco-Friendly Packaging Options
With growing environmental concerns, many liquid packaging machines are now compatible with biodegradable and recyclable materials, aligning with the global shift towards sustainability.
IoT and Remote Monitoring
The integration of IoT in packaging machines allows for remote monitoring and predictive maintenance, which minimizes downtime. Operators can access data on performance and potential issues, making troubleshooting faster and more efficient.
Customization for Specific Needs
An increasing trend toward customizable liquid packaging machines allows companies to select machines tailored to their specific products and operational needs. This adaptability ensures that each machine aligns with the business’s production scale and product characteristics.
Conclusion
Liquid packaging machines are indispensable for industries dealing with large volumes of liquid products, ensuring efficiency, consistency, and adaptability across diverse applications.