Are you struggling with inefficiency and inaccurate filling in your production process? Inconsistent manual liquid filling could lead to a lot of waste and unhappy customers. The solution is to build a 5ml to 30ml liquid filling machine with precision and automation.
To build a 5ml to 30ml liquid filling machine, start with a peristaltic pump and a variable-speed motor for precise control. Add a digital flow meter, adjustable bottle guides, and sensors for automation.
Keep reading to learn how you can build a custom liquid filling machine to meet your specific needs.
Step 1: Choose the Right Peristaltic Pump
When it comes to filling small quantities of liquid, peristaltic pumps are perfect because they are accurate, hygienic, and can handle a wide range of liquids without contamination. These pumps work by squeezing a flexible tube, which forces the liquid out. This means the liquid never comes into contact with any of the pump’s internal parts, which makes them great for sensitive liquids like pharmaceuticals, cosmetics, and food products.
For a 5ml to 30ml filling machine, you need to select a pump that supports this range of volumes. Look for a pump that has an adjustable flow rate so you can easily switch between different filling volumes. This is especially important if you have different types of products you produce like liquid soap, essential oils or food additives.
Key Considerations:
- Select a pump that can handle the desired flow rate, typically adjustable between 5ml to 30ml.
- Ensure the tubing material is compatible with the liquid you intend to fill.
- Consider a pump that is easy to clean, as this will minimize downtime during product changes.
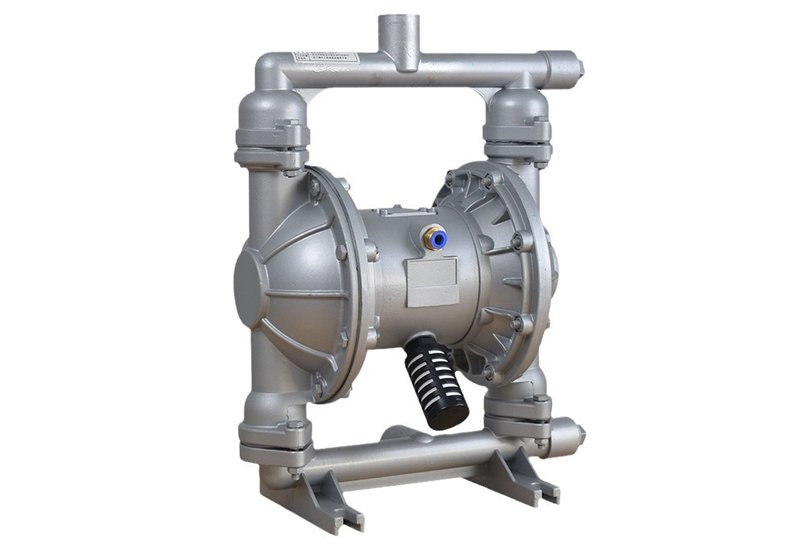
Step 2: Implement a Variable-Speed Motor
You’ll need a motor with variable speed control to change the speed of the pump. This allows you to adjust the filling rate based on the viscosity of the liquid and the size of the bottles you are filling. The motor controls how fast the liquid comes out, so you can fill quickly without making a mess or under filling the bottles.
Benefits of a Variable-Speed Motor:
- Adjusts filling speed for different liquids (e.g., thicker liquids like honey versus thinner liquids like water).
- Helps control the filling accuracy, ensuring that the correct volume is dispensed every time.
- Reduces operational wear on the machine by preventing overloading the pump.
For precision control, use a motor controller with easy-to-adjust settings for different speeds based on your production needs. This way you can use the same machine for different liquid products, similar to what you need for powder filling capping machines.
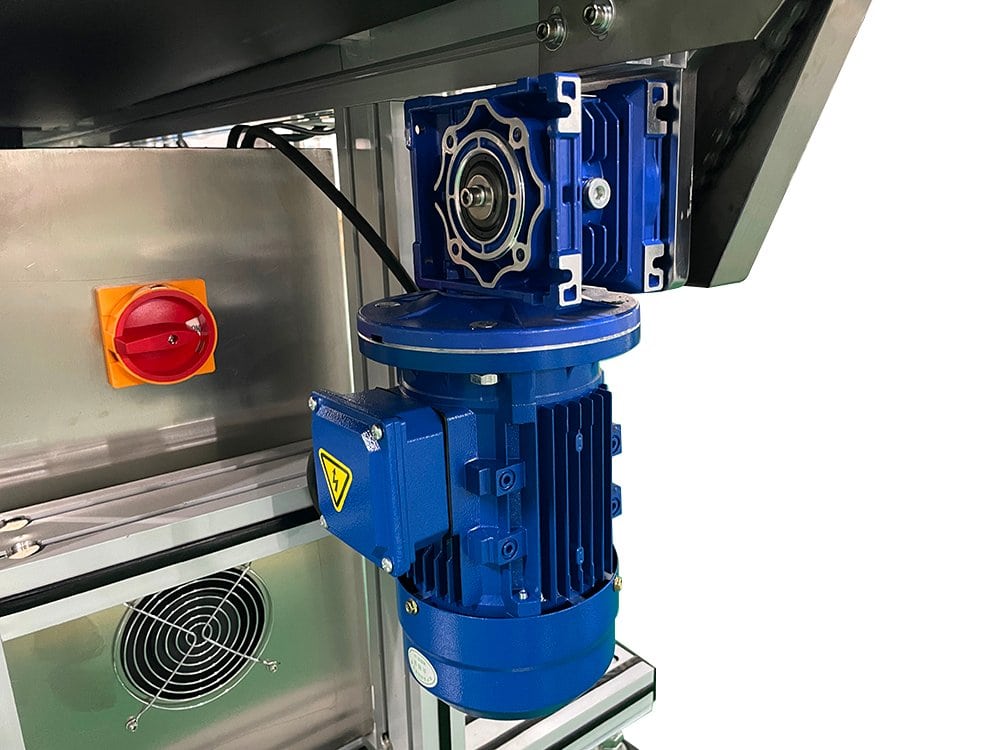
Step 3: Design a Flexible Bottle Platform
You need to be able to fill different sizes of bottles, so you need to design a flexible platform. You will need adjustable guides on the platform to hold the bottles in place. These guides will allow you to fill bottles from 5ml to 30ml. It will also keep the smaller bottles from tipping over during the filling process.
Features of the Bottle Platform:
- Adjustable guides to accommodate various bottle diameters and heights.
- A sturdy platform made of non-corrosive materials to withstand repeated use and exposure to liquids.
- Optional add-ons like clamps or supports for odd-shaped bottles.
A flexible platform allows you to fill different sizes of bottles without changing parts or making major adjustments to the machine, similar to the adjustable platforms used in powder filling machines for different size containers.
Step 4: Automate the Process with Sensors
Automation is essential if you want to improve the efficiency of your filling machine. You can add bottle detection sensors to start and stop the filling process when a bottle is under the dispensing nozzle. This eliminates the need for someone to press a button to start and stop the filling process.
Sensor Types to Include:
- Proximity Sensors: Detect the presence of a bottle and trigger the filling process automatically.
- Level Sensors: Ensure the correct amount of liquid is filled based on the bottle size.
- Flow Sensors: Monitor the liquid flow rate to ensure that the set volume is dispensed accurately.
Adding sensors turns your machine into a semi-automatic or fully automatic system, taking the human error out of the equation and speeding up the filling process. This is similar to what you need for the automatic filling and capping machines where you use sensors to make the process consistent and precise.
Step 5: Ensure Precision with a Digital Flow Meter
For any liquid filling machine, accuracy is critical. By including a digital flow meter, you can monitor the flow rate in real time. This will ensure that the machine dispenses the right amount of liquid every time. Flow meters are important when dealing with different viscosities because the amount of liquid they dispense changes based on the flow rate of the liquid.
Advantages of a Digital Flow Meter:
- Real-time monitoring: Keep track of the liquid flow and adjust the rate as needed.
- Accurate dosing: Prevents overfilling or underfilling, ensuring compliance with industry standards.
- Flexibility: Can be adapted to various liquids and production speeds, just as digital flow meters are utilized in powder filling capping machines to control the flow of powders.
Integrating a digital flow meter will ensure that your machine maintains a high level of accuracy, regardless of the type of liquid being filled.
Step 6: Consider a Ready-Made Smear Liquid Filling Machine
While building a custom liquid filling machine can be fun, you may want to look at buying a small liquid filling machine as a faster alternative. There are machines that are specifically designed to fill small amounts of liquid, and they come with features like adjustable filling volumes, sensors for automation, and easy-to-use controls.
Benefits of Ready-Made Filling Machines:
- Time-Saving: Reduces the time spent on design and testing.
- Reliability: Built-in components designed for precision and efficiency.
- Cost-Efficient: May end up being more cost-effective than building a custom machine from scratch.
Step 7: Test and Calibrate the Machine
Once you have built or purchased your machine, you need to test and calibrate it before you start using it for production. Run tests using different liquids and different size bottles to make sure the machine fills each bottle correctly. You may need to adjust the speed, the sensitivity of the sensors, and the flow rate to get the best performance.
Calibration Tips:
- Run multiple tests with the maximum and minimum bottle sizes to ensure flexibility.
- Adjust the sensors and flow meter to handle different liquid viscosities.
- Perform regular maintenance and recalibration to keep the machine functioning at its best.
Testing and calibration are essential steps that ensure your machine performs consistently, much like the maintenance required for powder filling machines to keep them in peak condition.
Conclusion
Building a 5ml to 30ml liquid filling machine is a matter of planning and having the right components, including a peristaltic pump, a motor with variable speed, a digital flow meter, and bottle detection sensors. If you follow these steps and do regular maintenance, you will have a very efficient and precise filling machine.