If you are in charge of a manufacturing business, you must be well aware of the importance of equipment in producing products.. Companies strive to produce high-quality products quickly, and automation equipment plays a crucial role in achieving this goal. One essential piece of equipment in many industries is the labeling machine. These machines ensure that products are properly labeled, which is vital for brand recognition, compliance, and consumer information.
Labeling machines work by automatically applying labels to products or packaging. They can handle various label types and sizes, and they operate at high speeds to keep up with production demands. These machines use advanced technology to ensure precision and consistency, making them indispensable in many industries.
Understanding how these machines function can help you appreciate the technology behind them and how they contribute to modern manufacturing.
What Are the Main Components of a Labeling Machine?
Labeling machines consist of several key components that work together to apply labels accurately. The main parts include the label applicator, the conveyor system, and the control unit.
The label applicator is the part that dispenses and applies the label to the product. It uses a sensor to detect the product and then applies the label in the correct position. The conveyor system moves the products through the machine, ensuring a smooth and continuous process. The control unit manages the overall operation, coordinating the applicator and conveyor system for optimal performance. These components must work in harmony to ensure that labels are applied correctly and consistently, minimizing errors and downtime.
How Does a Labeling Machine Ensure Precision?
Precision is crucial in labeling, as incorrect or misaligned labels can lead to compliance issues and damage brand reputation. Labeling machines use various technologies to ensure accuracy.
Sensors and cameras are often used to detect the position of products and labels, ensuring that labels are applied at the correct spot. Additionally, many machines have feedback systems that adjust the application process in real-time to correct any deviations. The use of high-quality materials and precise engineering also contributes to the overall accuracy and reliability of the machine. With these technologies, labeling machines can achieve high levels of precision, making them essential for industries where accuracy is paramount.
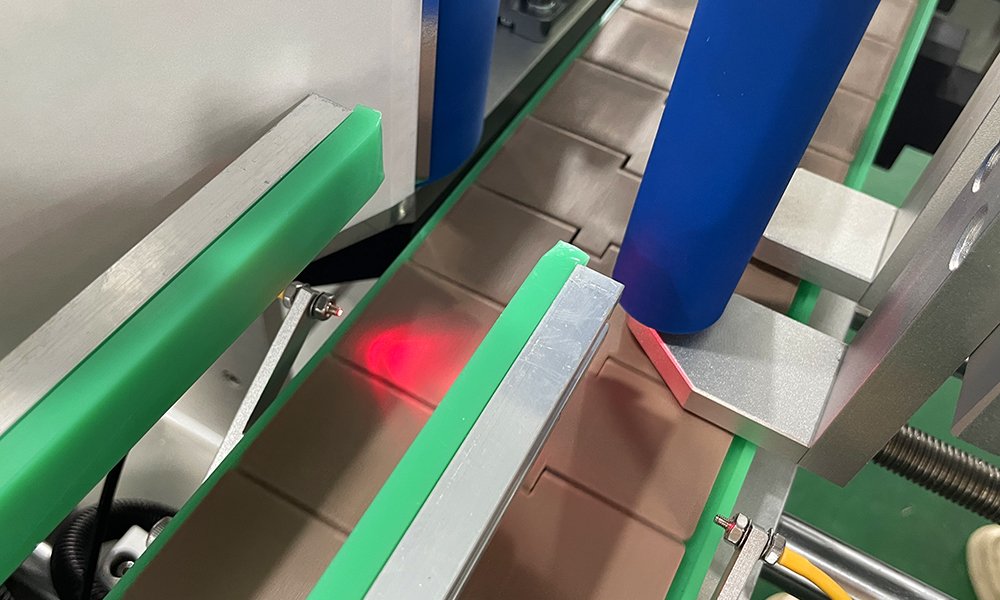
What Types of Labeling Machines Are Available?
There are several types of labeling machines, each designed for specific applications. Common types include pressure-sensitive labeling machines, hot melt glue labeling machines, and cold glue labeling machines.
Pressure-sensitive labeling machines use adhesive labels that stick to products when pressure is applied. These machines are versatile and can handle a wide range of label types and sizes. Hot melt glue labeling machines use heated adhesive to apply labels, providing a strong bond that is ideal for products exposed to harsh conditions. Cold glue labeling machines use liquid adhesive, which is suitable for applications where hot glue might damage the product. Choosing the right type of labeling machine depends on the specific needs of your production process and the characteristics of your products.
What Are the Benefits of Using Labeling Machines?
Labeling machines offer numerous benefits that make them a valuable addition to any production line. One of the primary advantages is increased efficiency. Automated labeling can significantly speed up the production process, reducing the time and labor required to apply labels manually.
In addition to efficiency, labeling machines improve accuracy and consistency. By applying labels precisely, these machines help maintain brand integrity and ensure compliance with regulations. They also reduce the risk of errors and rework, leading to cost savings and improved overall productivity. These benefits make labeling machines a worthwhile investment for manufacturers looking to optimize their operations.
How Do Labeling Machines Adapt to Different Products?
Labeling machines are designed to be flexible and adaptable, capable of handling a wide variety of products and packaging types. This versatility is achieved through adjustable components and advanced control systems.
For example, the height and position of the label applicator can be adjusted to accommodate products of different sizes and shapes. Some machines also have interchangeable parts that allow for quick and easy changes between different label types. Advanced control systems enable the machine to switch between different labeling modes and settings, ensuring that each product is labeled correctly. This adaptability makes labeling machines suitable for diverse manufacturing environments, from small batch production to large-scale operations.
What Are the Maintenance Requirements for Labeling Machines?
Proper maintenance is essential to keep labeling machines running smoothly and to extend their lifespan. Regular cleaning and inspection of the machine’s components can prevent issues such as label jams and adhesive buildup.
Routine maintenance tasks include checking and replacing worn parts, calibrating sensors, and ensuring that the control unit is functioning correctly. Many labeling machines come with built-in diagnostic tools that alert operators to potential problems, making it easier to address issues before they lead to downtime. By following a regular maintenance schedule, manufacturers can ensure that their labeling machines operate efficiently and reliably.
How Can Labeling Machines Be Integrated into Existing Production Lines?
Integrating a labeling machine into an existing production line requires careful planning and coordination. The machine must be positioned correctly to ensure smooth product flow and synchronization with other equipment.
During integration, it’s important to consider factors such as the speed of the production line, the type of products being labeled, and the layout of the facility. Many labeling machines come with modular designs that make it easier to fit them into different production environments. Additionally, working with experienced technicians can help ensure a seamless integration process. Proper integration can enhance the overall efficiency of the production line and maximize the benefits of the labeling machine.
What Are the Latest Innovations in Labeling Machines?
The field of labeling machines is constantly evolving, with new technologies and innovations emerging regularly. Recent advancements include the use of smart sensors, IoT connectivity, and machine learning algorithms.
Smart sensors enhance the precision and reliability of labeling machines by providing real-time data and feedback. IoT connectivity allows machines to be monitored and controlled remotely, improving efficiency and enabling predictive maintenance. Machine learning algorithms can optimize the labeling process by analyzing data and making adjustments to improve performance. These innovations are driving the future of labeling machines, making them more efficient, reliable, and adaptable than ever before.
Conclusion
Labeling machines are a critical component of modern manufacturing, offering efficiency, precision, and versatility. By understanding their operation and benefits, manufacturers can make informed decisions about integrating these machines into their production lines. As technology continues to advance, labeling machines will undoubtedly become even more essential in the quest for high-quality, efficient manufacturing.